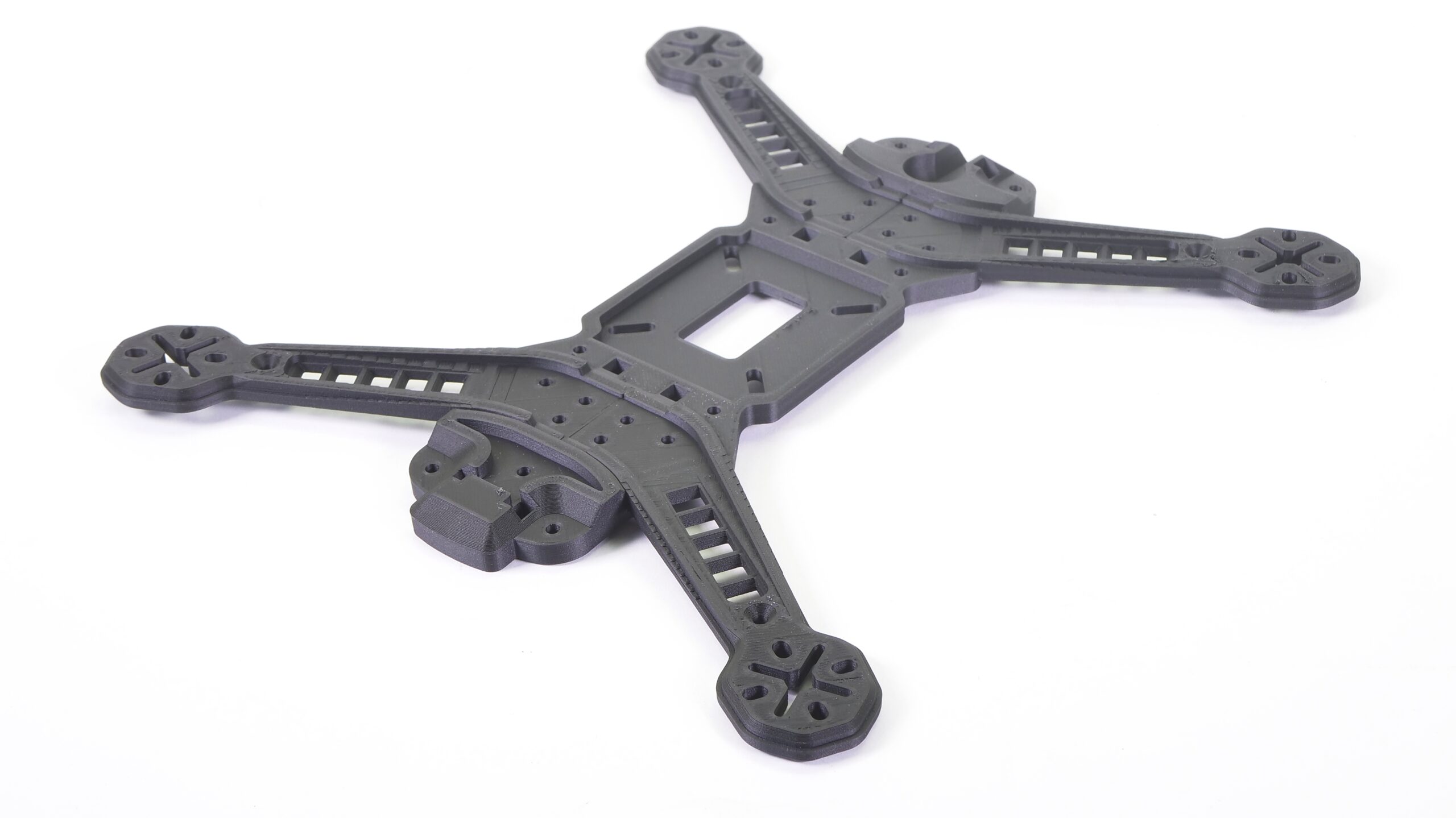
Basic info
Description
Carbon, glass or kevlar fibers are mixed with various polymers in order to improve their mechanical properties. Some of our Prusaments are altered this way: PA (Nylon), PC Blend and PP. Prusament PETG Carbon Fiber black is filled with carbon fibers too, but just for aesthetic purposes. Fibers (in general) inside the filament improve its dimensional stability, making it lightweight and less susceptible to warping. It also increases high-temperature resistance and tensile yield strength but it usually decreases Charpy impact resistance and layer-to-layer adhesion. Printing temperatures are slightly higher than for unaltered filaments. Some cheap filaments may have worse print characteristics, for example, often nozzle clogging, oozing, and filament breaking.
To compare supported material properties, see our material table.
Pros |
Cons |
---|---|
✔ Good abrasion resistance |
✖ A hardened steel nozzle is needed |
✔ Dimensional stability |
✖ Filament more brittle |
✔ Printing temperature is similar to single material filaments |
✖ Worse layer-to-layer adhesion |
✔ Nice look |
✖ Higher risk of nozzle clogging |
✔ Better high-temperature resistance |
|
Best use
Composite filaments can be used for making a vast range of components. This includes both hobby and professional uses, such as RC models (drone frames, airframes, car parts, etc.), the aircraft industry (functional prototypes) and the automobile industry (functional prototypes). Some filaments can even be used for scientific purposes due to their extreme resistance to heat, chemicals, etc. (Prusament PP and PA11, for example).
Tips for successful printing
Use a hardened nozzle
Carbon, glass and kevlar fibers are highly abrasive, so it is necessary to use a hardened nozzle.
Clean the nozzle before printing
It’s good to make cold pull before printing to make sure that the nozzle is clean.
First layer settings
The first layer should be perfectly fine, otherwise, you risk the nozzle clogging. The higher the layer height is and the wider the nozzle diameter is, the lower the chance of clogging the nozzle. The lowest optimal values are 0.4mm nozzle diameter and 0.2mm layer height.
Print surface preparation
Print surface preparation depends on the filament type. See our material table to find out more.
Sample prints
![]() | ![]() |
RC drone frame | Turbine |
![]() | ![]() |
Turboprop | Vial stand |
6 comments
https://us.polymaker.com/products/polymide-pa12-cf
Polymaker Polymide PA12-CF
what settings i should use?
and with CF we need to increase the temp 10 degrees above preset, i tried eSun PLA with generic pla preset but increase 10 degrees on hotend temp.
can I use Fiberology PA12-CF15 preset from prusaslicer? do i need to modify the preset hotend temp (increase 10 deg) too?